CASE STUDY
OUR CLIENT
Established in Japan in 1946, MITSUBA Corporation has a long history of excellence providing quality electrical components for automobiles. They have since expanded to over 50 facilities in 18 countries worldwide, establishing the plant in Monroeville, Indiana in 1997. Comprising about a quarter-million square feet, the Indiana Plant specializes in the production of wiper systems, electric power steering motors, and power sliding door systems for several automobile manufacturers.
MITSUBA President, Yuichi Nagase, has declared their “number one priority is thorough quality assurance and a stable supply of products, which are our fundamental business practices.”
THEIR OBJECTIVE
The MITSUBA Indiana Plant team sought a way to implement their President’s desire to take customer satisfaction to the next level. As a supplier of automotive components that are installed by the manufacturer during vehicle assembly, one error in a MITSUBA component can halt the entire assembly process and be extremely costly to their customer. Therefore, reducing the number of components with errors would directly correlate to an increase in customer satisfaction.
MITSUBA utilizes their own motor, control, and mechanism technologies for their production processes. Because these customized production areas are frequently adjusted due to advances in technology, they required a solution that could be easily modifiable. The Indiana Plant also desired a cost-effective solution that could be implemented across their 20+ production areas.
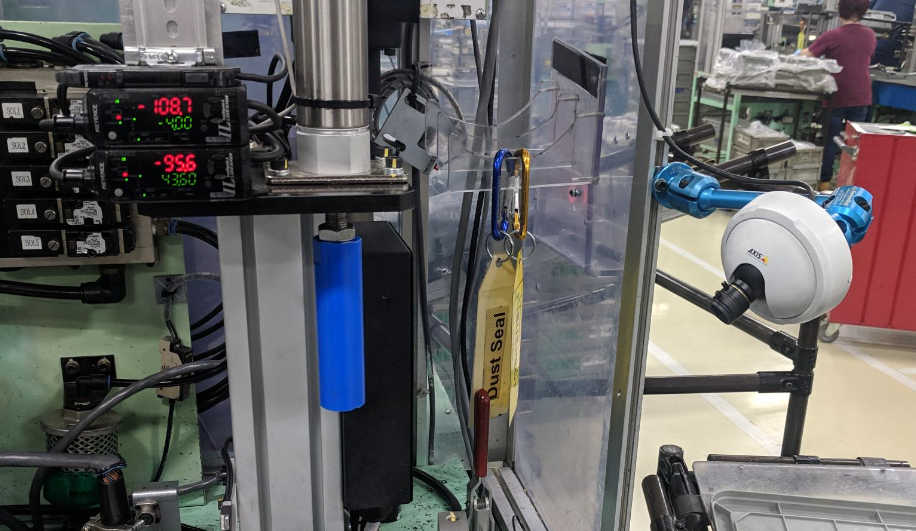
“We’ve struck a gold mine! We’ve been able to catch errors like never before. We now have the ingredients for a well-oiled machine.” -Dave Falater
OUR SOLUTION
The NWOSS Team came up with a solution to maximize quality assurance in production areas using the AXIS FA Series camera system and Milestone VMS. The AXIS FA Series system consists of a main unit, the FA54, that can connect up to four modular-style cameras.
Dave Falater, North American IS Director for MITSUBA, said his team mounts the modular-style cameras directly on the production lines and can easily adjust their views to allow plant management to zoom in on a particular process. Using Milestone, plant management is able to view historical video for each production area.
The quality and frame rate of the video provides details on the smallest of deviations. If an error is observed, the video displays the component’s serial number with time stamp so plant management can locate the faulty component quickly. Plant management can then make any necessary adjustments to the components, equipment, and processes to perfect the overall production.
SUCCESSFUL RESULTS
Falater described a scenario in which the camera system had an immediate impact on quality assurance: spotting a bolt that was being installed slightly off vertical in one of their components. Plant management was able to quarantine the affected parts. Then they fine-tuned the production equipment to eliminate future errors.
In the year since the solution has been implemented, the MITSUBA Corporation Indiana Plant has not received a single complaint on product quality issued by a customer. “We’ve struck a gold mine! We’ve been able to catch errors like never before. We now have the ingredients for a well-oiled machine,” said Falater.